Imagine a wire that can withstand extreme temperatures, resist harsh chemicals, provide excellent electrical insulation, and reduce friction to a minimum. Such a wire exists, and it's called the etched PTFE wire. In this article, we will explore more details about this remarkable product.
Etched PTFE wire is a specialized type of wire that is manufactured using a process called etching. PTFE, which stands for polytetrafluoroethylene, is a high-performance fluoropolymer known for its exceptional properties. By subjecting PTFE wire to an etching process, the surface of the wire is modified, enhancing its capabilities and making it suitable for a wide range of demanding applications.
What is Etched PTFE Wire?
Etched PTFE wire is a type of wire that has undergone a surface modification process called etching. Etching involves chemically treating the surface of the wire to create a roughened texture. This process increases the surface area of the wire, improves its adhesion properties, and enhances its functional characteristics.
Etched PTFE wire is widely used for high-temperature NTC lead wire, and the conductor is silver plated nickel wire or silver plated copper wire. It has good soldering characteristics to NTC chips (Glass Head NTC) and PTFE insulation after etching. It has good bonding characteristics to epoxy powder, perfectly solving conductor soldering to chips, and insulation bonding to epoxy powder of NTC.
Etched Teflon wire can be divided into several kinds of wires according to its insulator material, such as FEP, PFA, PTFE, and ETFE. Etched PTFE wire is one type of etched Teflon wire. The insulating surface of ordinary PTFE wire is very smooth. If this wire needs to be bonded to epoxy powder, it will cause poor adhesion. Our etched PTFE wire greatly improves this situation. After the etching process, the surface of the PTFE becomes rough and covered with a layer of small holes, which significantly improves the adhesion between the PTFE layer and epoxy powder.
Advantages of Etched PTFE Wire
High-Temperature Resistance
One of the primary advantages of etched PTFE wire is its exceptional resistance to high temperatures. PTFE is known for its ability to withstand extreme heat, and this resistance is further enhanced through the etching process. Etched PTFE wire can operate reliably at temperatures exceeding 200°C (392°F), making it ideal for applications where traditional wires would fail.
Chemical Resistance
Etched PTFE wire exhibits excellent chemical resistance. It is resistant to a wide range of corrosive substances, including acids, bases, solvents, and oils. This resistance makes etched PTFE wire suitable for applications in chemically aggressive environments, such as chemical processing plants, laboratories, and industrial settings.
Electrical Insulation Properties
Another notable advantage of etched PTFE wire is its exceptional electrical insulation properties. PTFE is an excellent insulator, and the etching process further improves its dielectric strength. Etched PTFE wire can effectively withstand high voltages, making it a reliable choice for electrical and electronic applications where insulation is crucial.
Low Friction Coefficient
Etched PTFE wire has a low friction coefficient, offering reduced resistance to motion. This property makes it suitable for applications where low friction is desired, such as in moving parts or mechanisms. The low friction coefficient of etched PTFE wire contributes to improved efficiency, reduced wear and tear, and enhanced performance in various applications.
Applications of Etched PTFE Wire
Medical Devices
In the medical field, etched PTFE wire is commonly used in devices such as catheters, endoscopes, and surgical instruments. Its biocompatibility, high-temperature resistance, and chemical inertness make it suitable for applications where contact with bodily fluids and harsh sterilization methods are involved.
Aerospace Industry
The aerospace industry demands wires that can withstand extreme temperatures, exposure to fuels and lubricants, and high electrical loads. Etched PTFE wire meets these requirements, making it an ideal choice for aircraft wiring, avionics, and space exploration equipment applications.
Electronics and Telecommunications
In the electronics and telecommunications sectors, etched PTFE wire plays a crucial role. It is used in high-frequency cables, coaxial cables, and microwave applications. Its low dielectric constant and excellent signal transmission properties make it suitable for high-speed data transfer and telecommunications infrastructure.
Automotive Industry
In the automotive industry, etched PTFE wire finds applications in wiring harnesses, sensors, and engine components. Its ability to withstand high temperatures, resistance to automotive fluids, and excellent electrical properties ensure reliable performance in demanding automotive environments.
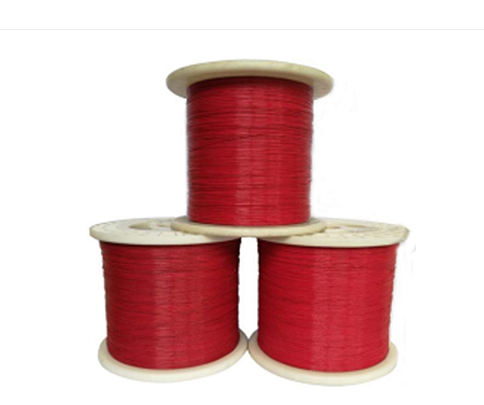
Manufacturing Process of Etched PTFE Wire
- Wire Preparation: High-quality PTFE wire with precise dimensions is selected for the process.
- Cleaning: The wire undergoes thorough cleaning to remove any contaminants and ensure optimal adhesion during the etching process.
- Etching: The wire is immersed in a chemical solution that selectively etches the surface, creating a roughened texture.
- Neutralization: After etching, the wire is neutralized to stop the etching process and remove any residual chemicals.
- Drying: The wire is carefully dried to ensure the complete removal of moisture.
- Quality Control: The etched PTFE wire undergoes rigorous quality checks to ensure it meets the required specifications before being released for use.
Factors to Consider when Choosing Etched PTFE Wire
Temperature Requirements
Evaluate the temperature range to which the wire will be exposed and ensure that the chosen etched PTFE wire can withstand those temperatures without compromising its performance.
Chemical Environment
Consider the specific chemicals the wire will come into contact with and verify the wire's resistance to those substances. Different etched PTFE wires may have varying levels of chemical resistance.
Electrical Properties
Assess the electrical requirements of your application, such as voltage, current, and insulation requirements. Choose an etched PTFE wire with suitable electrical properties to ensure safe and efficient operation.
Mechanical Strength
Consider the mechanical stresses and forces the wire will experience. Ensure that the chosen etched PTFE wire has the necessary tensile strength and flexibility to withstand the application's demands.
Conclusion
Etched PTFE wire is a remarkable solution for demanding applications that require high-temperature resistance, chemical resistance, excellent electrical insulation, and low friction. Its unique properties make it a preferred choice in medical devices, aerospace, electronics, telecommunications, and automotive industries. By understanding the manufacturing process, considering the application requirements, and choosing the right etched PTFE wire, you can ensure optimal performance and reliability in your specific use case.